AUVENTS ALVEOLAIRES | DU SUR MESURE POUR LA STATION GNV DE GRENOBLE
Nous avons su répondre aux exigences du distributeur français de gaz naturel pour véhicules, ENGIE, pour l’équipement de la station GNV du Marché d’Intérêt National de Grenoble. Notre tôlerie fine a relevé le défi d’une fabrication sur mesure et d’envergure de 2 auvents alvéolaires, en acier.
1
Le défi : fabriquer 2 auvents alvéolaires en acier, d’une hauteur de 6 mètres
- Grâce à notre formidable outil industriel et notre bureau d’étude le TF Lab, nous avons répondu positivement à la sollicitation de ENGIE Solutions pour fabriquer deux auvents alvéolaires de 6 mètres de haut. Une fabrication tout en précision et sur mesure pour notre atelier de tôlerie fine.
GNVERT, l'offre de mobilité durable gaz naturel d’ENGIE Solutions, distribue et commercialise du GNV (carburant gaz naturel pour véhicules) depuis plus de 20 ans et propose des solutions de mobilité durable aux collectivités et entreprises qui souhaitent réduire leur impact environnemental.
-
45 jours
d’études au TF Lab
-
625 heures
de fabrication
-
10.3 Tonnes
d’acier et aluminium
Pour relever le défi, l’équipe TF FACTORY a entendu et respecté les exigences du cahier des charges de son client
- Respect de l’encombrement au sol
- Respect des exigences techniques de ventilation du toit pour prévenir les risques liés à la rétention de gaz
- Respect de la forme proposée par le cabinet d’architecture
- Allégement de la structure métallique pour rendre la structure plus aérienne, légère, plus simple, plus minimale
- Respect de la charte couleur de la marque
2
-
Le TF Lab, une formidable équipe
Le bureau d’étude intégré de TF FACTORY travaille en collaboration étroite avec l’équipe commerciale. Il est en charge de la conception, de l’étude de faisabilité et de la mise sur plan préalables à toute phase de production.
Notre équipe d’experts a écouté et pris en compte l’intégralité des besoins du client. Grâce à une grande expertise métier, l’équipe a réalisé un prédimensionnement des épaisseurs de métal, elle a intégré une étude de la portance, de l’inclinaison du toit et des matières, puis, dans un second temps, des notes de calcul (normes de descente de charge, de résistance vent et neige et normes sismiques).
De la réception du dessin à la validation des plans par le client, le TF Lab a livré en 45 jours, l’étude de faisabilité des 2 auvents et les plans optimisés pour le lancement de la production.
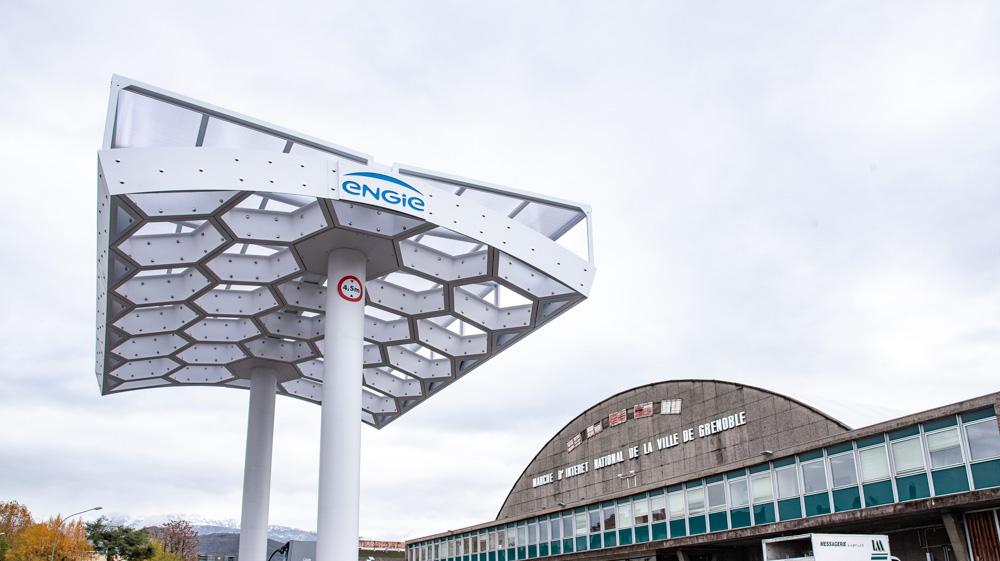
TF FACTORY, un catalyseur de succès
L’équipe du TF Lab a mis sur plan le projet, lui a donné une dimension matérielle et quantitative. Elle a fait le choix d’une conception par modules préfabriqués au sein de l’atelier de tôlerie fine, puis assemblés sur place. Ce système présente plusieurs avantages qui facilitent la fabrication, les finitions, le transport et l’assemblage des pièces métal sur site.
Les auvents se composent d’une répétition d’un même module alvéolaire conçu sur-mesure, assemblés et surmontés d’une toiture en panneaux polycarbonates soutenus par deux piliers en acier.
Le partenariat avec TF Factory permet à Engie Solutions de se positionner comme un acteur différenciant, sur le marché des Stations GNV.
La solution mise au point par le TF Lab permet à ENGIE Solutions de proposer un auvent innovant : très robuste tout en donnant une impression visuelle de légèreté. C’est un bel objet architectural qui s’intègre parfaitement dans le paysage urbain grenoblois. Grâce à sa forme différenciante, ce modèle d’auvent a une allure esthétique, qui se différencie largement des modèles classiques plutôt massifs et fonctionnels.
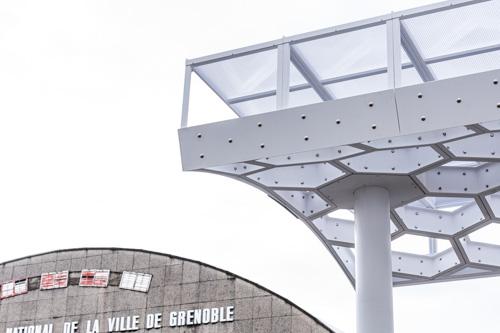
3
Une fabrication sur mesure
Le processus de fabrication se structure en différentes phases, et commence avec la transformation de la matière première : l’acier.
- Transformer l’acier
Les plaques d’acier de 6 et 8 mm sont découpées au laser, ébavurées et pliées manuellement. Les alvéoles sont décomposées en 2 parties pliées puis assemblées ensuite par soudure.
Les piliers en acier sont galvanisés afin de renforcer leur résistance à la corrosion et aux dégradations potentielles en milieu urbain.
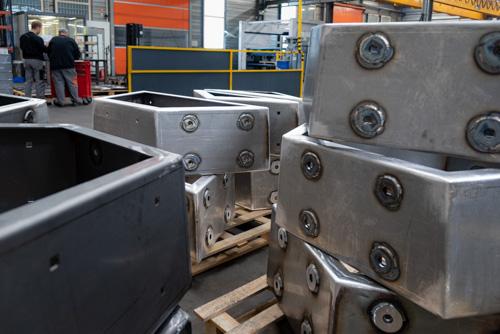
- Souder l’acier
Les pièces découpées et pliées intègrent ensuite les étapes d’assemblage, elles sont traitées par un chaudronnier expérimenté. A partir des directives du plan, il réalise toutes les opérations de mise en forme et d’assemblage par soudage.
Pour garantir une haute qualité de fabrication de A à Z, TF Factory travaille main dans la main avec sa filiale Beirens, spécialiste de la chaudronnerie de gros gabarit. Cet atelier a pris en charge l’assemblage et les finitions des piliers, soit les opérations de soudage et de mise en peinture.
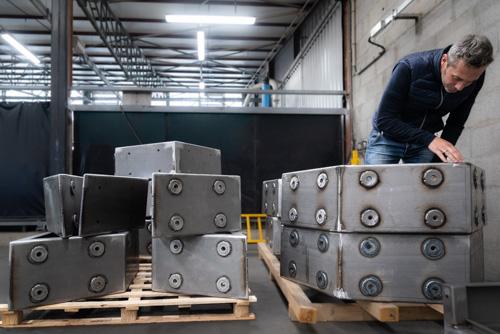
- Conformité
Un montage à blanc avant peinture est réalisé dans l’atelier de tôlerie fine TF Factory. C’est une opération essentielle qui permet de vérifier la conformité des pièces fabriquées sur-mesure par TF Factory. Cette opération valide également l’équilibre de l’arche et la cohérence du jeu de montage sur site, qui sera réalisé hors atelier, pendant la phase du chantier d’implantation.
- Peindre l’acier
La chaine de peinture intégrée offre une autonomie totale à TF Factory, jusqu’à la fin de la production
Après assemblage, toutes les pièces alvéolaires rejoignent le secteur peinture, pour une préparation avant mise en couleur. L’équipe prépare la pièce à peindre avec un traitement de surface, puis une primaire adaptée au besoin. La poudre époxy est directement projetée sur la surface métallique en la répartissant sur une couche mince et uniforme. Après le poudrage, les pièces sont placées dans un four à haute température afin de figer et durcir la poudre.
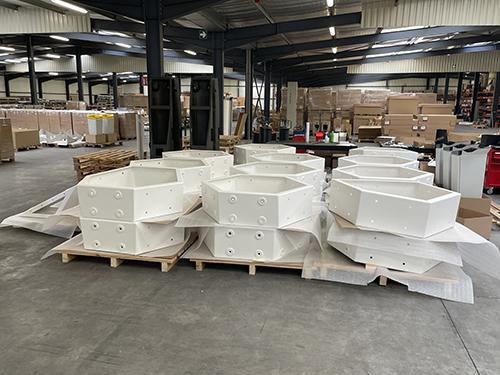
4
Installation sur le site du Marché d'Intérêt National de Grenoble
Après 330h dans l’atelier peinture, les pièces sont prêtes pour l’expédition. Les auvents rejoignent leur site d’implantation, par camions sur lesquels ils sont chargés en pièces détachées.
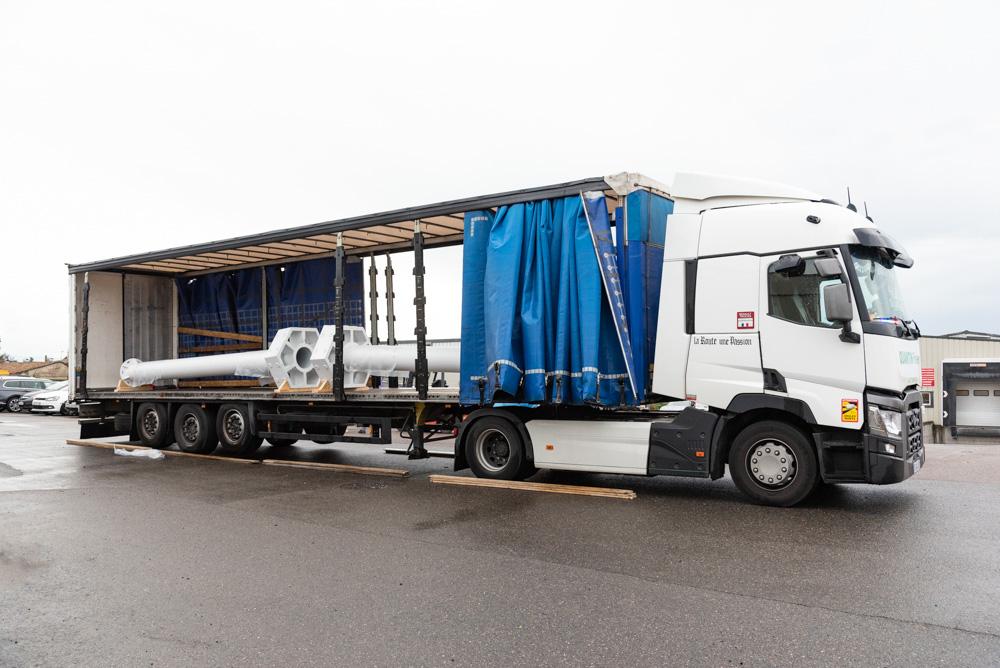
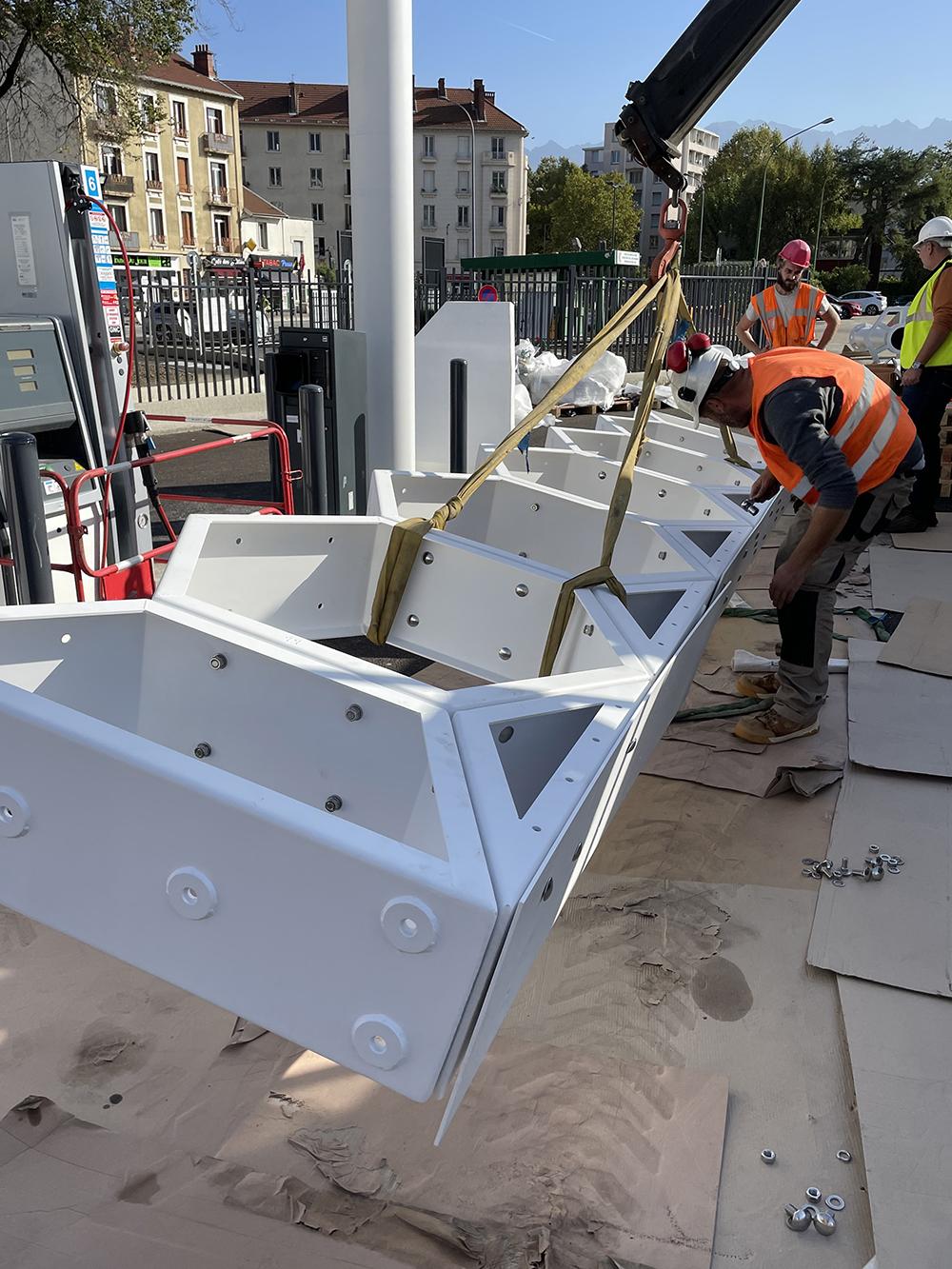
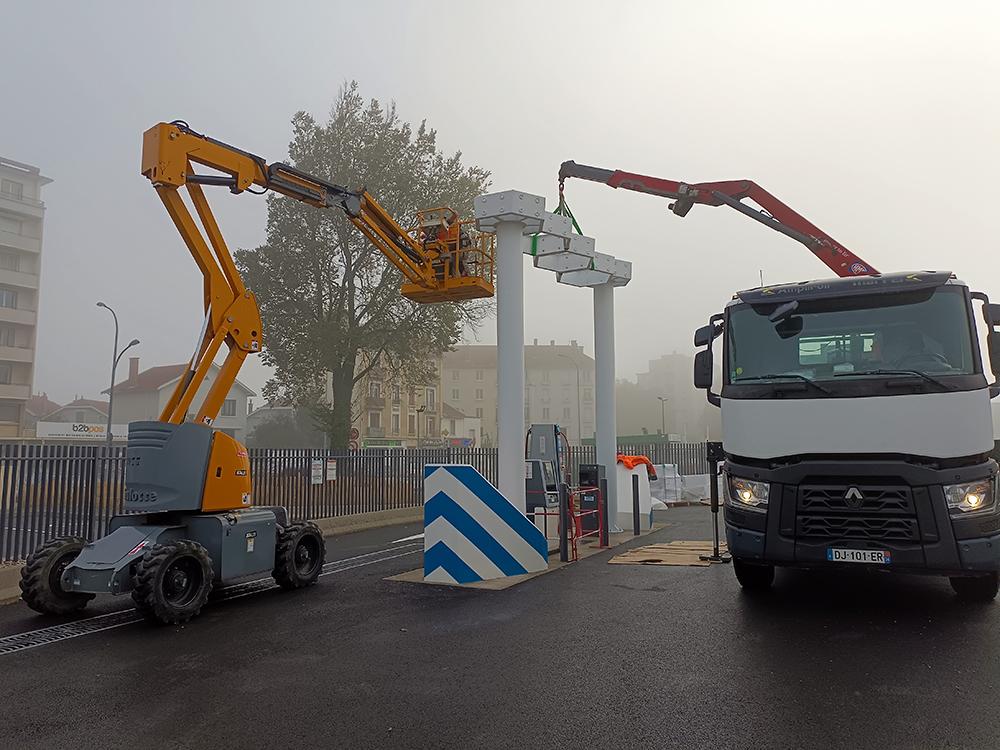
5
-
La petite histoire
-
Pourquoi un auvent alvéolaire ?
Les alvéoles donnent une allure légère et aérienne aux auvents. Elles permettent d’aérer et de ventiler la toiture pour prévenir les risques de rétention du gaz.
Dessinées par l’agence d’architecture Punk Agency, ces formes alvéolaires répondent à l’architecture en voile de béton armé de la grande halle du Marché d’intérêt national MIN de Grenoble, situé sur le même site.
Bâtiment aussi connu sous le nom de Marché de gros, construit en 1963 par Marcel Welti, architecte et directeur général des services techniques de la ville de Grenoble.
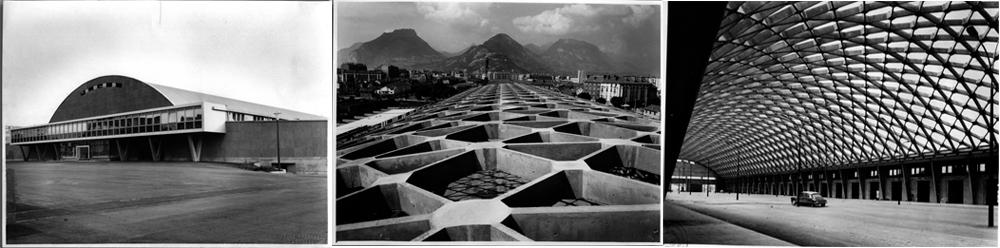
« Le bâtiment se compose d’une vaste halle couverte, caractérisée par sa voûte autoportante (d’une portée libre de 40 mètres, sur 160 mètres de long) surplombant la nef centrale. La structure du voile est constituée d’un treillis en béton armé formé d’arcs croisés, les uns perpendiculaires à l’axe principal, les autres formant un angle de 45 degrés avec les premiers. Ce treillis, recouvert de longues dalles translucides qui assurent l’éclairage naturel de l’édifice, est réalisé avec 728 éléments préfabriqués identiques. C’est une véritable prouesse constructive dans laquelle les maîtres d’œuvre ont su tirer profit de toutes les qualités du béton armé. Cet édifice est labellisé Architecture contemporaine remarquable. »
Source : Grenoble patrimoine
6
Inauguration de la station
Grenoble Alpes Métropole accélère la décarbonation de la mobilité avec une nouvelle station multi-carburant GNC/ BioGNC et recharge électrique au Marché d’Intérêt National.
Christophe Ferrari, Président de Grenoble Alpes Métropole, Eric Piolle, Maire de Grenoble et Jean-Baptiste Furia, Directeur de GNVERT, offre de mobilité au gaz naturel d’ENGIE Solutions, ont inauguré ce 13 décembre la station d’avitaillement en Gaz Naturel Comprimé (GNC) et BioGNC localisée au Marché d’Intérêt National (MIN) à Grenoble.
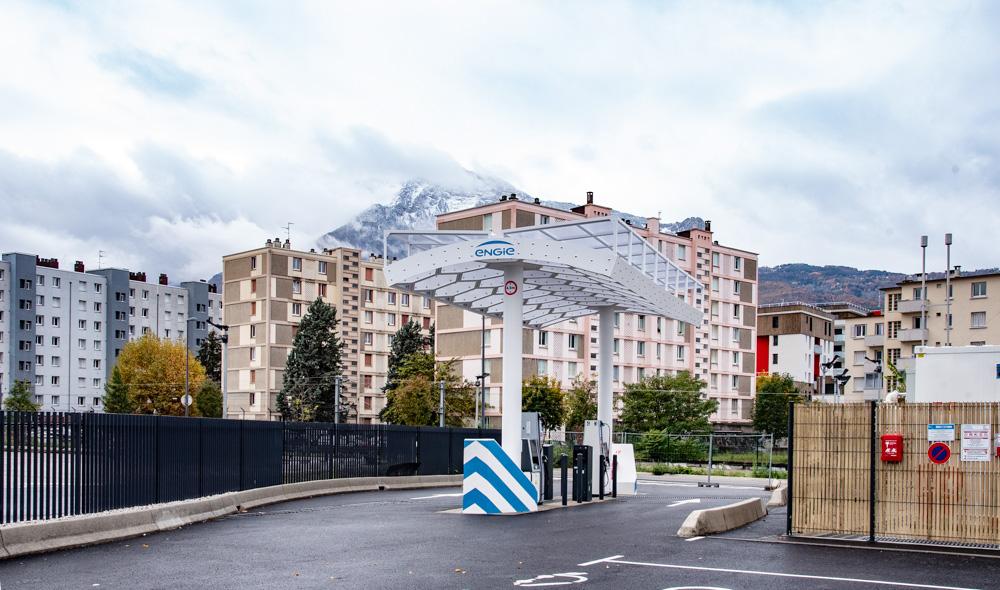